Ways Artificial Intelligence is Transforming the Fabrication Industry
Northwood explains how its latest breakthrough technology – AI-driven automation in the Raptor Saw Jet – boosts efficiency by reducing manual input and producing precise cuts
Raptor Saw Jet with the overhead camera. Photo courtesy of Northwood.
For more than 30 years, Northwood Machine has been a leader in CNC machinery for stone, wood and advanced materials. Renowned for its high-precision fabrication solutions, Northwood continues to drive the industry forward with cutting-edge technology. Its latest breakthrough? AI-driven automation in the Raptor Saw Jet -- revolutionizing stone fabrication by boosting efficiency, reducing manual input and delivering unmatched precision.
SW: What inspired the integration of AI into the Raptor Saw Jet, and how does it set this machine apart from others on the market?
RT: The integration of AI into the Raptor Saw Jet was driven by the need for enhanced precision, efficiency and real-time adaptability in stone cutting. Using Northwood’s proprietary algorithms, material data and tooling intelligence, this AI mimics human decision-making to optimize cuts and predict tool wear. As an AI-driven machine in the stone industry, it sets the Raptor Saw Jet apart by offering unmatched automation, reduced errors and higher productivity — ultimately resulting in superior cut quality.
SW: How does AI optimize slab orientation and tool pathing compared to traditional methods?
RT: Northwood AI, in conjunction with the Horus D2 Scanner, analyzes slab data, CNC tooling specifications and material-specific cutting guidelines to automatically generate the optimal cutting program. It determines tool placement, detects whether relief cuts are needed and adjusts cutting paths based on the material’s characteristics — creating a fully automated process.
In traditional programming, an operator must manually consider material density, type (engineered stone, quartzite, marble, etc.), saw blade selection, waterjet speed, spindle
RPM and cutting methods. They also have to decide on tool usage, material placement and the appropriate program, which increases the likelihood of errors. Northwood AI eliminates these manual decisions, providing process security, improved efficiency and consistent results while significantly reducing operator dependency.
SW: What specific challenges in slab cutting has AI helped solve, and how has it improved efficiency and precision?
RT: AI has addressed several challenges in slab cutting, particularly the need to accommodate the unique characteristics of different stone materials. Each type -- quartzite, marble, engineered stone, porcelain and Dekton — requires distinct cutting approaches, including adjusted feed speeds, RPMs, blade types and waterjet settings. Traditionally, different operators would apply varying techniques, leading to inconsistencies in cut quality.
With AI, these variables are standardized through material-specific algorithms that store optimized cutting parameters for each stone type. AI automatically adjusts feed speeds, selects the correct blade and applies the best cutting strategy — ensuring consistent, precise results every time. By removing human error from the equation, AI-driven processing enhances accuracy, reduces waste and accelerates turnaround times.
SW: How does this AI-enhanced workflow reduce the learning curve for new operators?
RT: AI-enhanced workflows, like those in the Northwood Raptor Saw Jet, significantly reduce the learning curve for new operators. With Northwood AI managing decision-making and programming, operators no longer need programming expertise. AI automatically processes material information and geometry layouts, eliminating the need for manual programming. This shift allows employees to spend less time on programming and more time on production, improving overall shop efficiency.
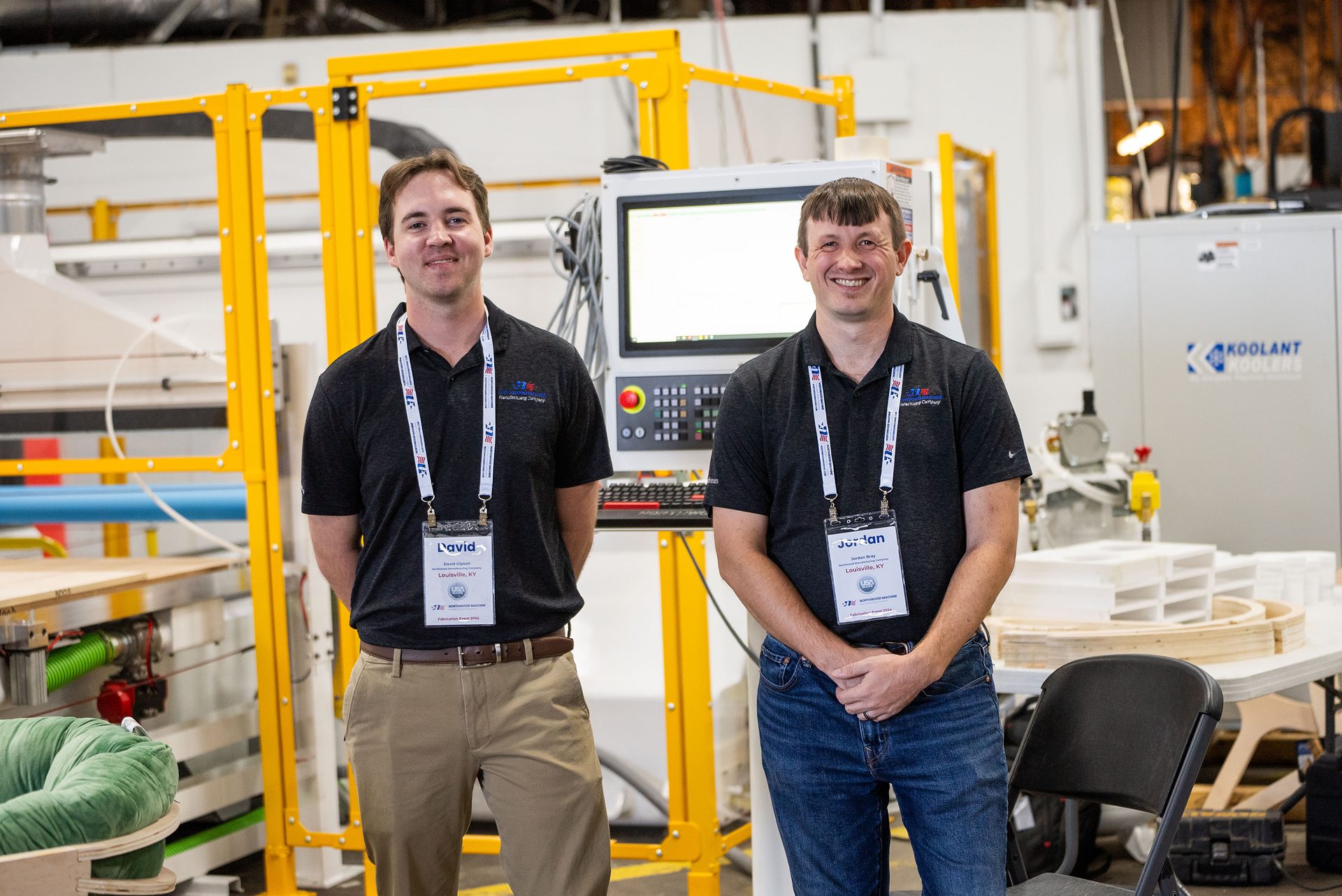
Northwood software engineers, David Gibson and Jordan Bray. Photo courtesy of Northwood.
SW: What feedback have you received from fabricators using this AI integration in real-world applications?
RT: Fabricators report that Northwood Machine’s Raptor Saw Jet:
- Simplifies operations by eliminating complex programming steps.
- Reduces manual input, allowing operators to focus on production.
- Minimizes errors, improving consistency across all cuts.
Boosts overall efficiency, increasing throughput and shop productivity.
SW: What’s next for AI in stone fabrication?
RT: In the coming months, Northwood AI will expand into CNC router programming, further automating fabrication processes and enhancing precision. AI-driven solutions are transforming the industry by eliminating guesswork, improving accuracy, and maximizing production efficiency, allowing fabricators to scale their businesses without increasing labor costs.
Rod Sigman CTC, CCTS, CSMTT is the business development leader for MAPEI Corporation’s UltraCare® line of products for the care and maintenance of tile and stone products. Sigman has a proven track-record of success in the flooring industry, with experience in both training and education, as well as all support functions pertaining to national sales accounts and distribution. He has served on the technical committees of the National Tile Contractors Association (NTCA) and the Natural Stone Institute (NSI). He has successfully completed the Ceramic Tile Consultant Course, is a Certified Ceramic Tile Specialist (CCTS) and is also a Concrete Slab Moisture Testing (CSMT) Technician. Further, he was recognized by the Marble Institute of America (now the Natural Stone Institute) as a significant influence for the stone industry.