NOVEMBER 2022
case study
Finding the Right Solution
Merkrete Pro Epoxy met the challenge to restore the travertine facade of the Nueces County Courthouse in Corpus Christi, TX
by Phillip Hall, marketing communications manager, Parax USA
Photos provided by Merkrete
By the time the first stone fell from the Nueces County Courthouse, its inhabitants were fully aware that the next rainfall would bring another leaky office and a fresh cradle for the creeping mold. The Corpus Christi moisture and sea air blowing in off the Gulf of Mexico had pushed through the building’s travertine facade and eaten away at the concrete substrate underneath, rotting the 12-story tower from the outside in. But as the 1- x 2-inch stone tile sloughed from the building’s decaying skin and cracked a triple-pane window on its way down, the danger to the public became inescapable.
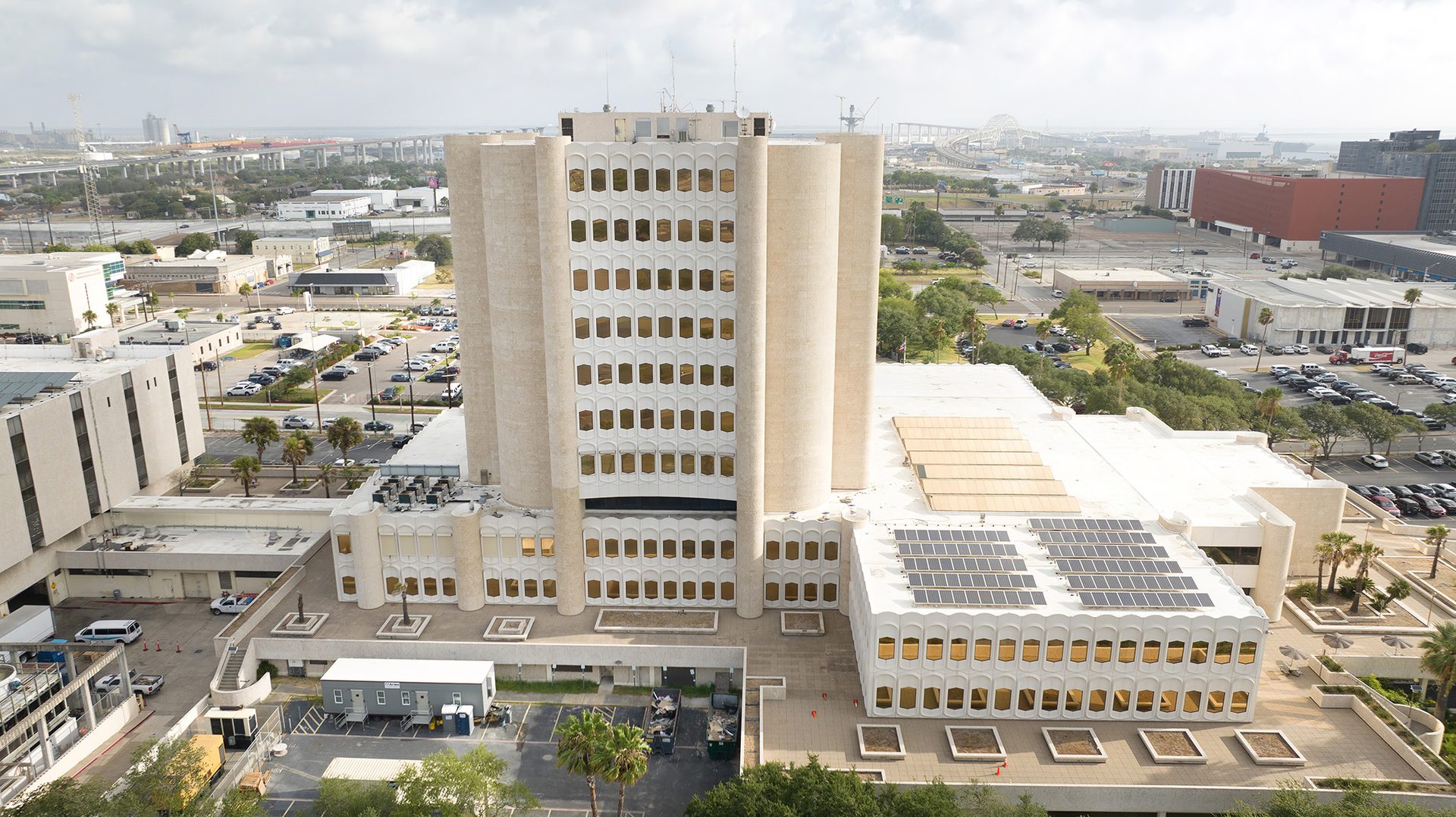
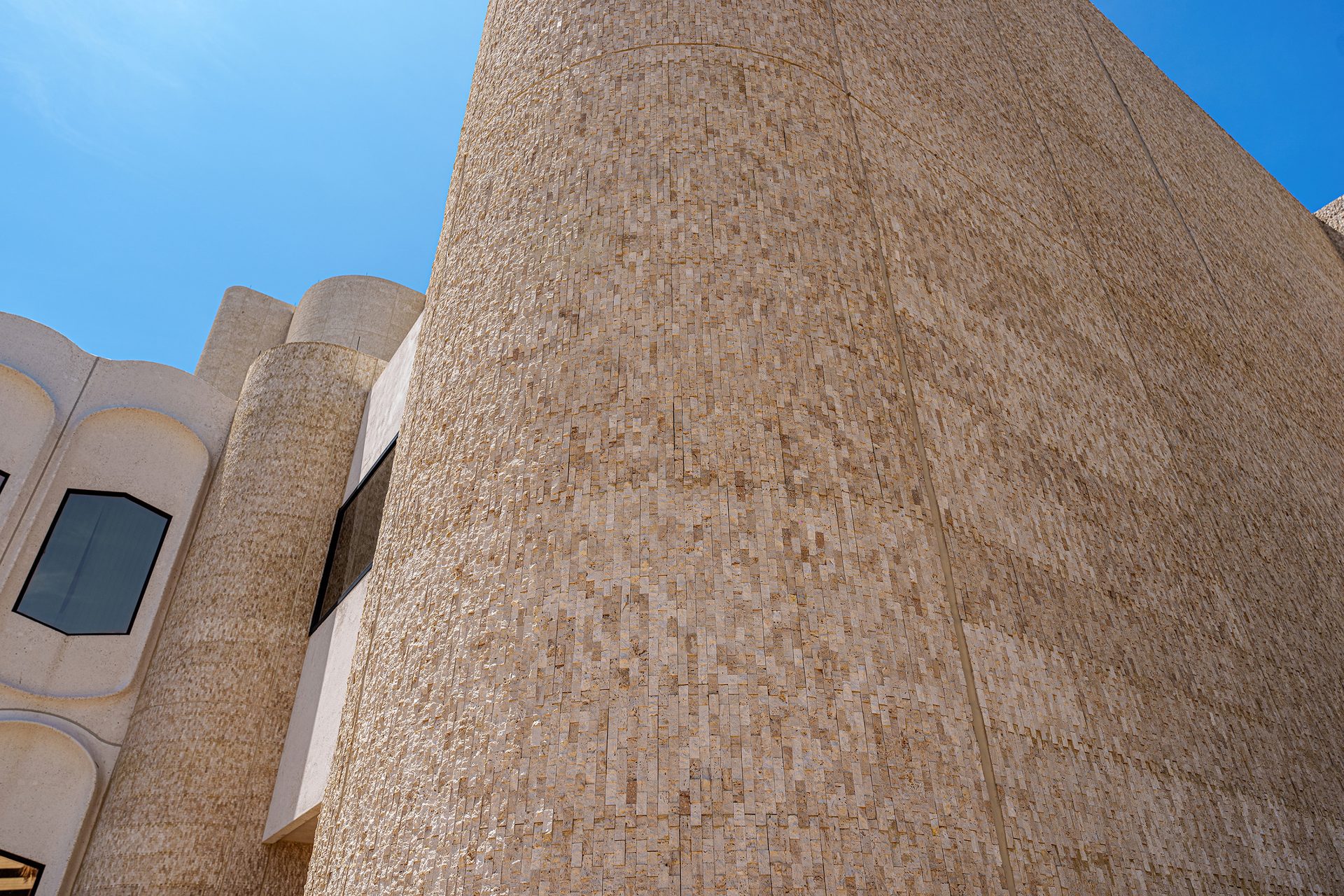
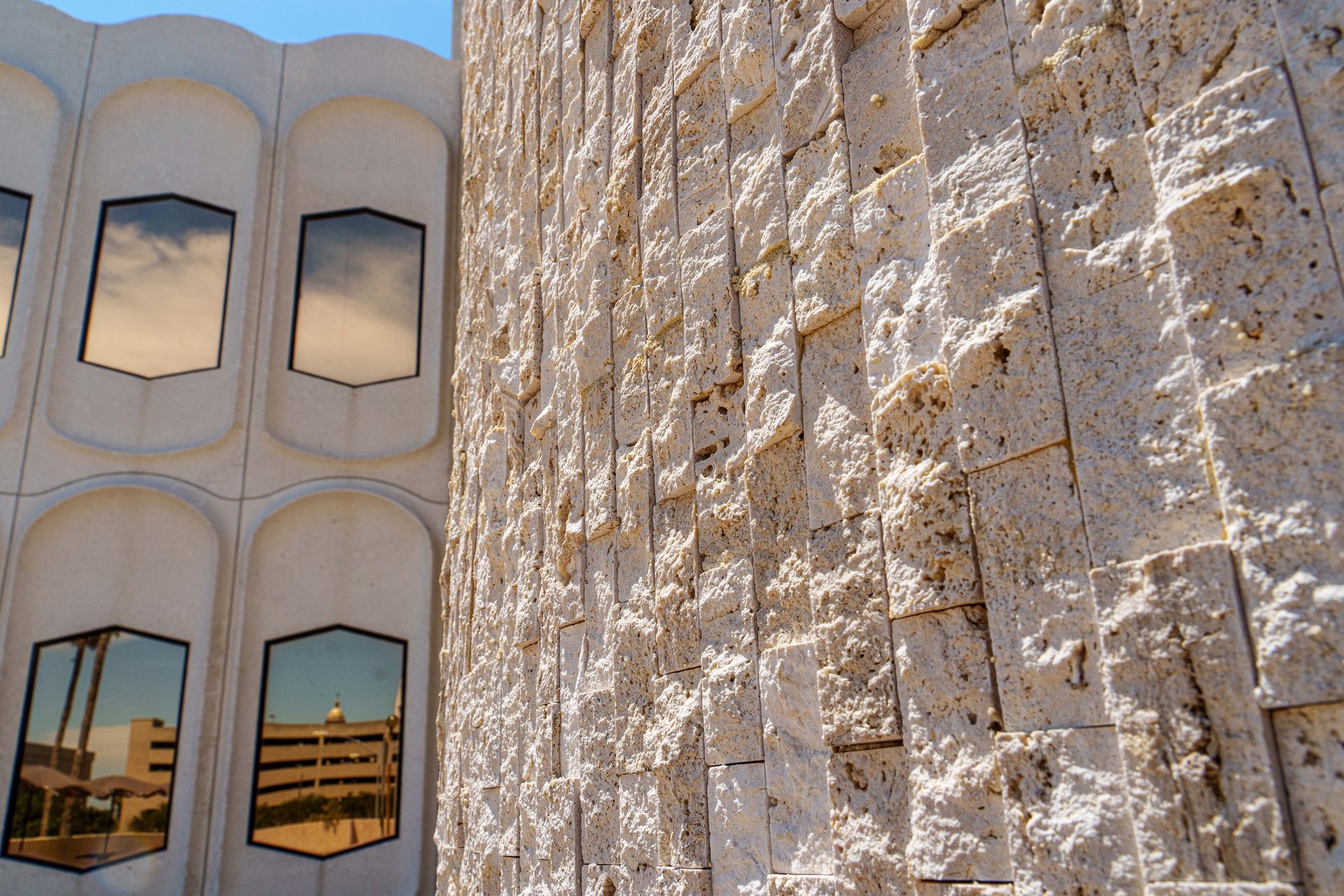
Restoring Order
When the $6.7 million restoration project was announced in February 2021, Richter Architects were determined to bring the courthouse back to its original glory. They planned to replace the existing tile with the same style after the cement substrate had been repaired. However, it was decided that the tile mortar needed a stronger bond than the one applied in 1977.
Richter Architects wrote in the project specifications that field adhesion testing would be conducted by an independent third-party testing agency. The mortar selected for the job would be required to have a minimum 50 psi tensile strength to securely hold the 51,000 square feet of tile to the concrete panels. Richter Architects commissioned Curtainwall Design Consulting (CDC) to perform the tests that would find the right solution for the restoration.
Building a Case
Frontier Waterproofing Project Manager Jordan Crider initially selected Merkrete 820 Dustless Merlite to test for the project. The mortar seemed a natural choice to set the mass of vertical tile due to its lightweight and durable bond. Crider’s team keyed in the mortar to the substrate and back-buttered the 12- x 12-inch resin sheets the stone tiles were attached to. The tiles were applied to the substrate where they would sit for 10 days.
On the day of the test, CDC epoxied a 1- x 2- x- 3/8-inch steel puck to the face of the tile. When the epoxy had cured, a ComTen puller tester was attached to the puck. The device applied a tensile load to the puck and tile at a rate of approximately 200 lb./min. until failure. To Crider’s dismay, the 820 Dustless Merlite did not meet the 50-psi mandate. The stone separated from the mesh around 35 psi.
Crider partnered with Merkrete technical sales manager Clint Anna to examine why the bond failed between the backside of the thin-set tile and the adhesive layer through the mesh. More importantly, the two worked to find a solution that would exceed the 50-psi minimum. Anna believed the same issue that was causing the original stone tile to fall away from the building was preventing the 820 Dustless Merlite from properly adhering the new tile to the concrete. “Not only did the mortar have to adhere to the stone; it had to adhere to the backing glue,” Anna concluded. “The resin that was on the tile sheet netting was breaking the bond with the mortar.”
Indeed, the 2021 TCNA Handbook backed up Anna’s assessment with its Fiberglass Mesh Reinforced Stone entry. It noted, “The adhesive used to attach the mesh … is commonly an epoxy or polyester-based resin to which Portland cement-based mortars will not reliably bond.” The entry continued, providing Anna with the solution he and Crider sought. “Such reinforced stone tiles require epoxy bonding mortar.”
Direct Examination
Anna and Crider entered Merkrete Pro Epoxy into the hunt for a suitable adhesive. Pro Epoxy is a three-component, 100-percent-solids epoxy compound that serves as both mortar and grout. Anna felt that its strong chemical resistance to many acids and alkalis would help the mortar withstand the environmental stressors certain to bombard the facade over the coming decades. Though, despite Pro Epoxy’s wealth of beneficial attributes, Richter Architects wanted to be certain the tile was set with the best solution in the industry, not just within Merkrete’s exhaustive portfolio.
It was decided that Merkrete’s Pro Epoxy would be tested alongside a top epoxy product from a leading global building materials provider. While similar to Pro Epoxy in many respects, the competing product was an attractive option due to its advertised lightweight formula. Between the two, CDC’s testing would determine which solution would be ideal for the Nueces County Courthouse.
It was decided that Merkrete’s Pro Epoxy would be tested alongside a top epoxy product from a leading global building materials provider. While similar to Pro Epoxy in many respects, the competing product was an attractive option due to its advertised lightweight formula. Between the two, CDC’s testing would determine which solution would be ideal for the Nueces County Courthouse.
The testing process was the same as that for 820 Dustless Merlite three weeks prior. The results, however, were far from alike. Out of 10 tests per product, the competing mortar exceeded the needed 50 psi in each. The average pull capacity for the mortar was a respectable 178 psi, topping out at 335 psi. Eight of the 10 tests resulted in “adhesive failure between stone/mesh,” meaning the mortar bond separated and released the stone.
Merkrete’s Pro Epoxy also greatly exceeded 50 psi on each test. Its average pull capacity was an unmatched 244 psi. The pull capacity reached as high as 395 psi -- nearly eight times the required results. While one of Pro Epoxy’s tests terminated due to adhesive failure from the 250-pound load applied, the other nine tests involved “cohesive stone failure.” Simply put, the adhesive maintained some or all its bond to the stone and the test concluded when the stone itself broke apart from the force applied. The total bond was retained in six of these tests, as the severed stone left behind its full mortar contact surface. Due to Pro Epoxy’s superior and consistent performance, it was chosen for the courthouse restoration.
Sustained
Though Pro Epoxy passed the tests for project selection, Richter Architects needed to be certain the Merkrete product would perform as impressively throughout the restoration project. The volume of tile to be installed on Nueces County Courthouse would ornament a blend of arcs and flat expanses with varying degrees of sun and wind exposure. These variables put a question mark on how well Pro Epoxy’s adhesion would hold from one surface to the next.
Starting two and a half months after Pro Epoxy’s first trial, CDC performed more than 30 additional pull tests to ensure consistent bonding. Beginning in September 2021 and concluding the following May, Pro Epoxy exceeded the required 50 psi of adhesion with every test, having the average tensile bond strength of 235.8 psi. The overwhelming majority of the tests ended with a stone cohesive failure or failure of the adhesive used to attach the puck to the travertine tile.
It was on the final round of pull tests when Pro Epoxy achieved its greatest result. CDC’s ComTen puller test applied 1,099 pounds of load to the test tile when the stone split, leaving the bonding surface intact. Richter Architects recorded a tensile strength of a staggering 550 psi -- 11 times the mandated pull. Had the stone not disintegrated from the pull load, Anna pondered, those in attendance would have witnessed the true upper limits of Pro Epoxy’s bond.
Doing Justice to Nueces County Courthouse
Frontier Waterproofing dedicated 20 tile setters to the courthouse for 10 months to deliver its new, secure facade. Anna and the team at Merkrete worked to provide Crider’s crew with Pro Epoxy in bulk to reduce the time spent opening and mixing the product. The equivalence of 3,400 commercial kits of Pro Epoxy is now tightly locking every travertine stone to the Nueces County Courthouse facade in what Crider acknowledged was the “biggest epoxy job we’ve ever done and probably ever will do.”
“This project is at the heart of our motto: It’s What’s Underneath that Counts,” said Merkrete Senior Product Manager Tom Carroll. “The reason we have such a wide array of tile-setting materials is because no two jobs are the same. On paper, our 820 Dustless Merlite would be the ideal mortar for the job, but something as simple as a resin mesh forced our partners at Frontier Waterproofing to rethink their materials and embrace our industry-leading epoxy. That’s why it is crucial for tiling contractors to work closely with a manufacturer that takes a strong interest in the success of their projects.”
Phillip Hall is Parex USA’s marketing communications manager, dedicating his efforts to the Merkrete brand of tile-setting systems. His time as a decorated, award-winning Navy journalist launched his career as a public relations, communications and marketing leader. Before Parex USA, Hall led many successful marketing teams in the fields of surveillance, cybersecurity and industrial computing.